Metal. Ceramic. Plastic.
Forged with Light.
Dax Research delivers advanced 3D printing, CNC machining, and laser welding solutions. Backed by a decade of expertise and partners like Schaeffler, we help bring complex designs into real-world production.
Services
What we do
From Metal 3D printing and machining to laser plastic welding
Laser Plastic Welding Consulting
Expert guidance on your laser plastic welding project.
From applications to production solutions.
CNC Machining
Precision CNC machining services for complex parts and components.
3D Printing Service Center
Professional 3D printing services with advanced materials and technologies.
Omnifusion3D Printer
Multi-material 3D metal printing system with precision laser fusion technology.
Laser Welding Tools & Applications
Advanced laser welding solutions for plastic components with exceptional precision.
Rapid Manufacturing
Streamlined production processes for faster time-to-market with reduced waste.
Show Room & Lab
Visit our facility to see our equipment in action and collaborate on projects.
Industries We Serve
Explore our expertise across various industrial sectors.
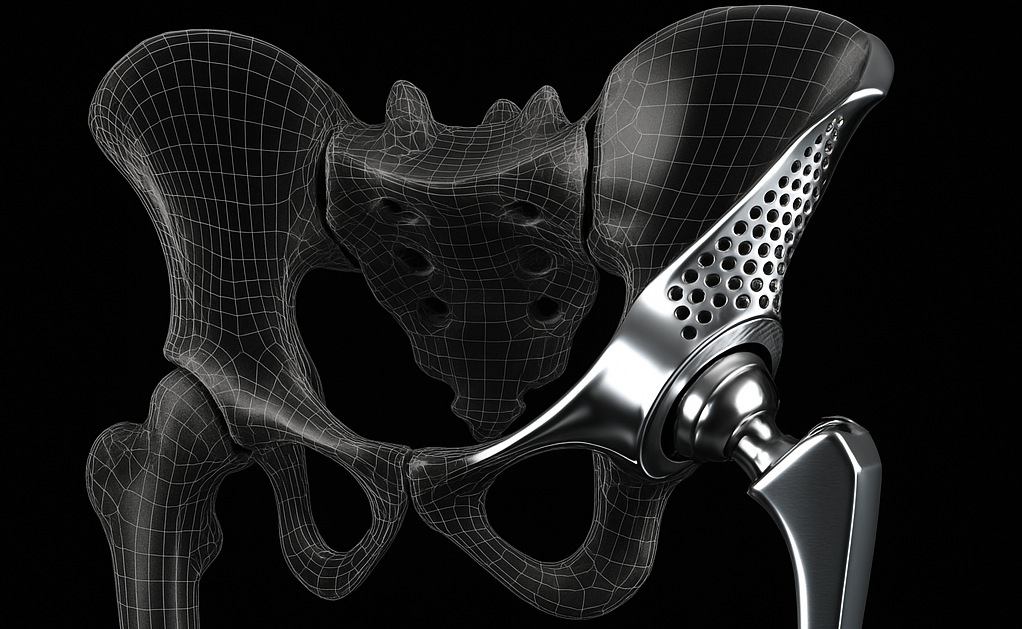
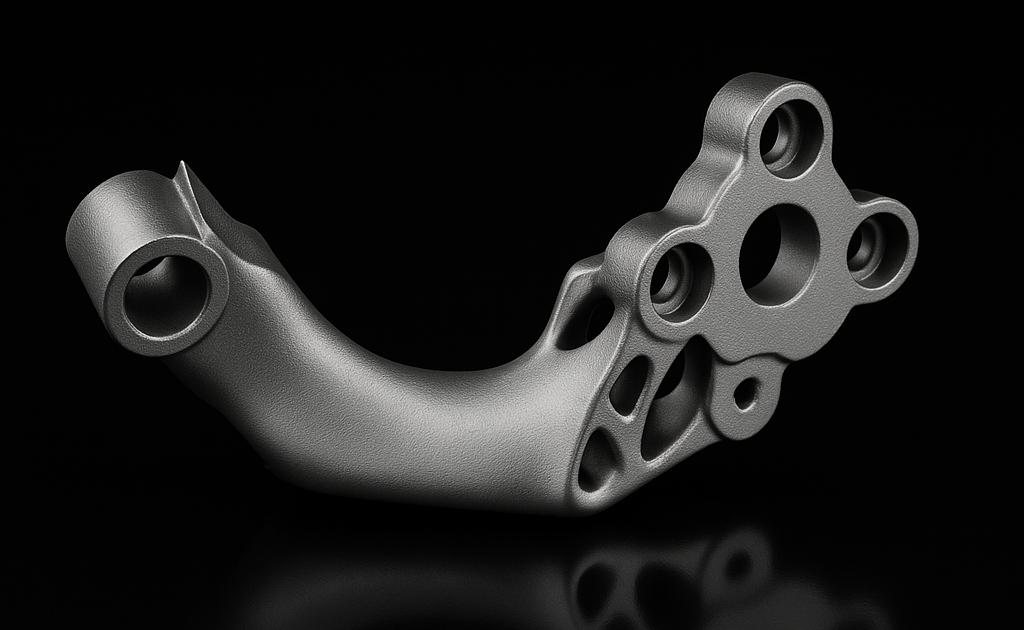
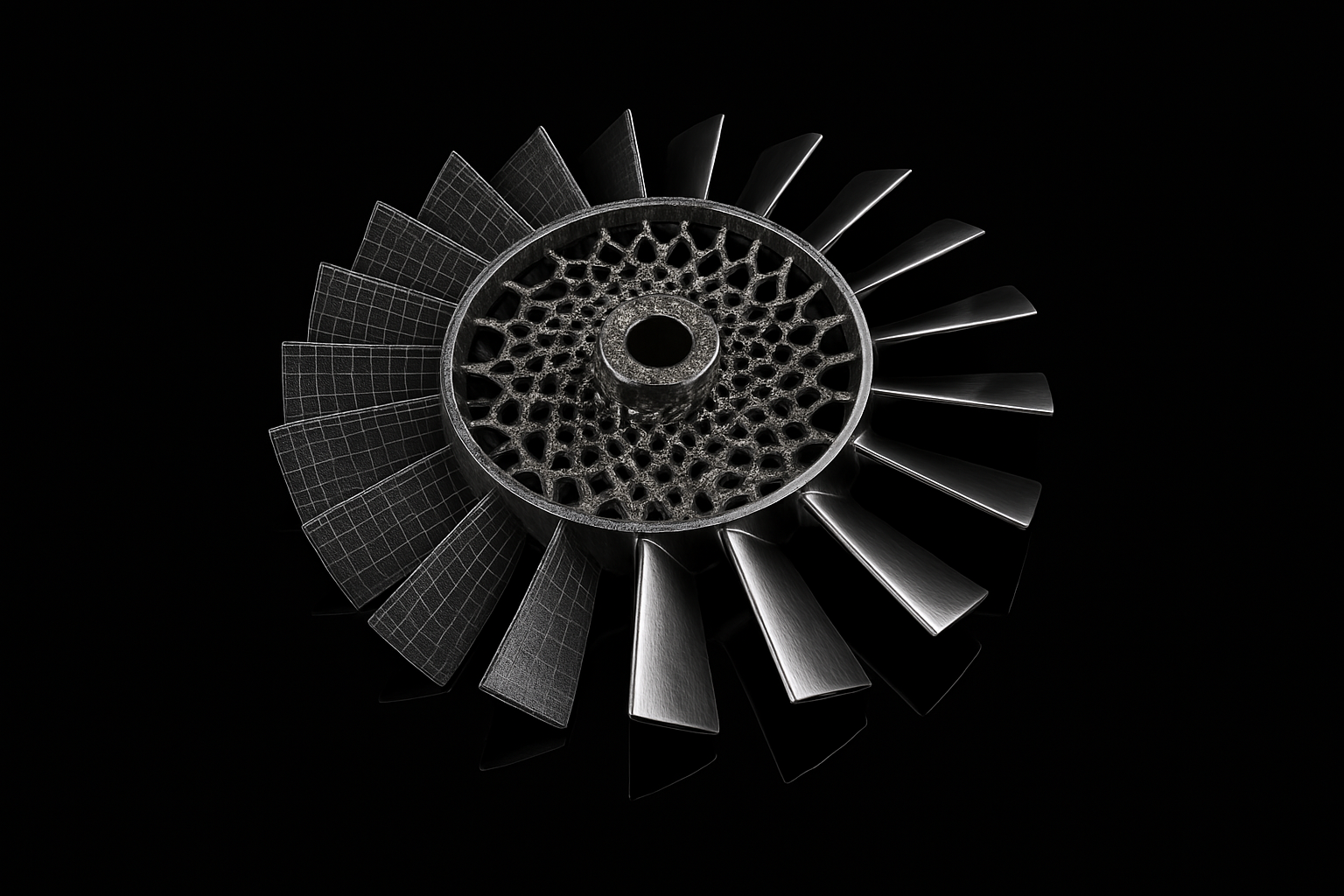
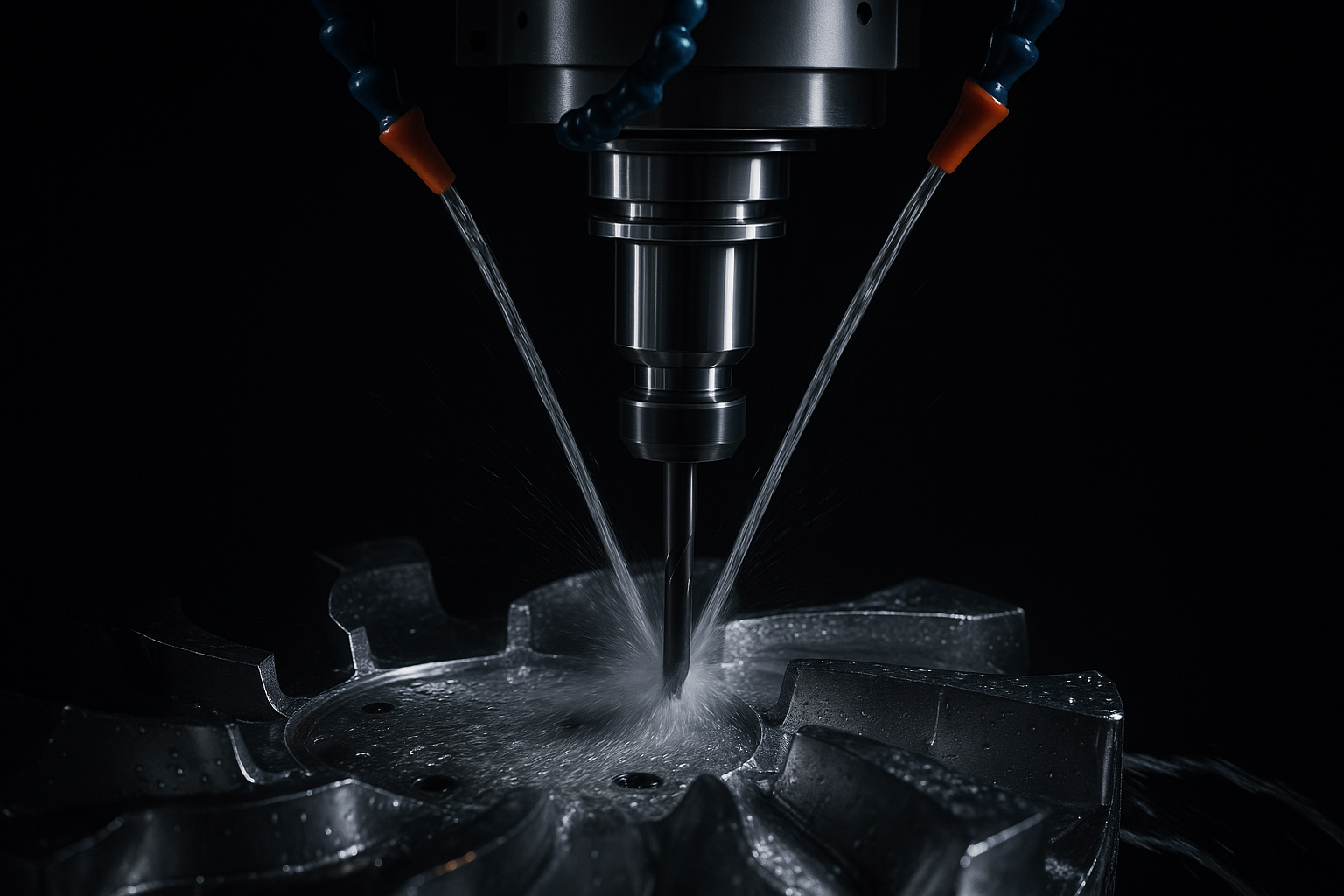
Introducing the Omnifusion3D Printer
Developed by Schaeffler, the Omnifusion3D represents the next generation in multi-material additive manufacturing
Unique Capabilities
- •Precision laser fusion with unprecedented accuracy
- •Advanced material compatibility for unique combinations
- •Innovative functional integration in products & tools
- •Flexibility in form for individual, free design
- •Reduced lead time, especially for tools & prototypes
Multi-Material Advantages
In many areas, additive manufacturing has established itself as an alternative to conventional production methods. Multi-material 3D printing opens up almost unlimited possibilities, offering:
- •Simplified production of components with complex geometries
- •Reduced material consumption and waste
- •Increased energy efficiency in production
- •More environmentally friendly material options
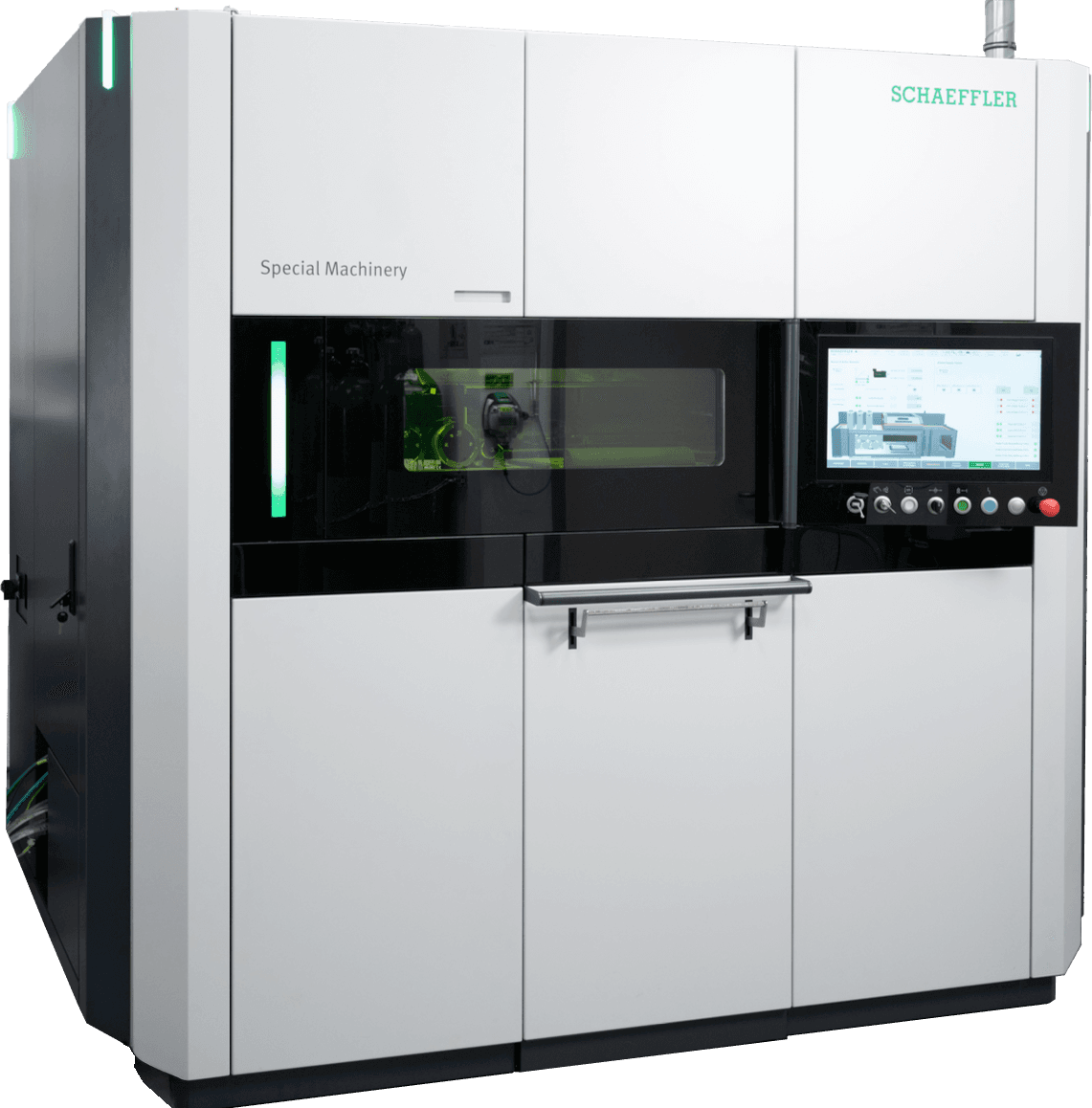
Technical Specifications
Specification | Details |
---|---|
Deposition width | 250 mm / 4.53 inches |
Layer thickness | 40 µm - 150 µm |
Recoating speed | Up to 50 mm/s / 1.97 inches/s |
Integrated powder containers | 750 ml per drum (3 drums) |
Recoater size | 480 x 361 x 182 mm / 18.9 x 14.2 x 7.2 inches |
Powder pixel resolution | 300μm for recoater and die filling platform |
Omnifusion3D Applications
Tool Components
Injection molding insert
- • High thermal conductivity
- • Fast availability of near-end-shape semi finish
- • Low waste of tool material
Welding brackets
- • High wear resistance and thermal conductivity
- • Minimal material waste
Products
Heat sink
- • Organic structure
- • High surface area for improved cooling
- • High thermal conductivity with lightweight housing
Medical implants
- • Innovative joint materials
- • Right material at the right place
Prototypes
Hydrogen applications
- • Increased integration level
- • Reduction of precious materials
- • Controlled porosity
Electric motor coil
- • Fully flexible design
- • Fast component availability
Get In Touch
Message me to discuss how I can help you with your laser welding, CNC machining or 3D printing needs.