Metal 3D
Printing Solutions
Production-grade, multi-material parts in days—powered by Laser Powder Bed Fusion up to 250 mm³.

Design Freedom
Print internal channels & lattices impossible with CNC.
Multi-Material Fusion
Combine copper, steel & ceramics—layer by layer.
Rapid Turnaround
Quote in minutes, ship parts in as little as 5 days.
Production Quality
≤ 99.8 % density, full CMM & CT inspections included.
Industries We Serve
Explore our expertise across various industrial sectors.
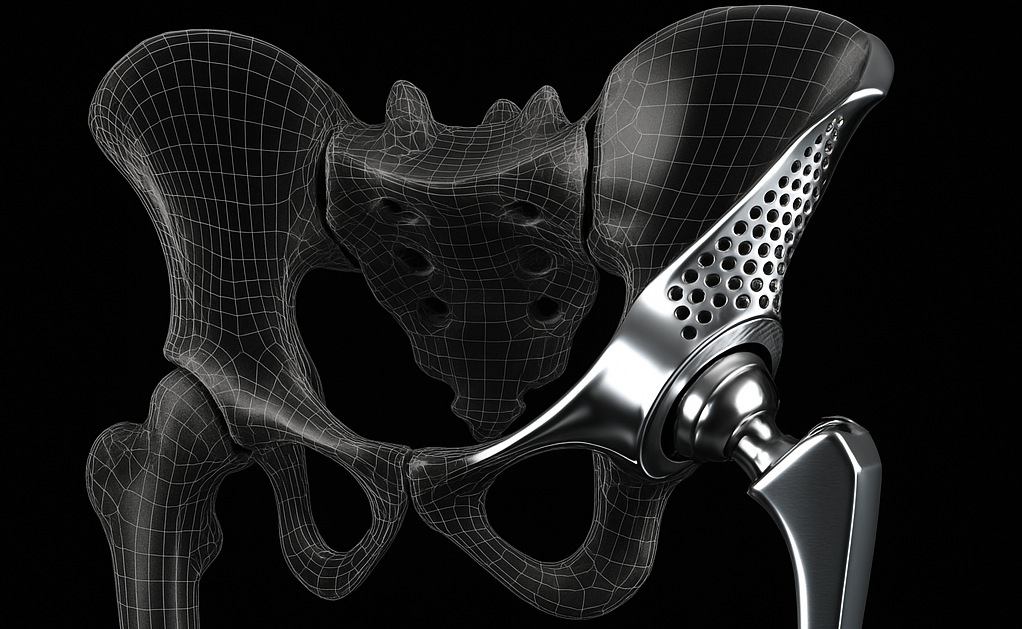
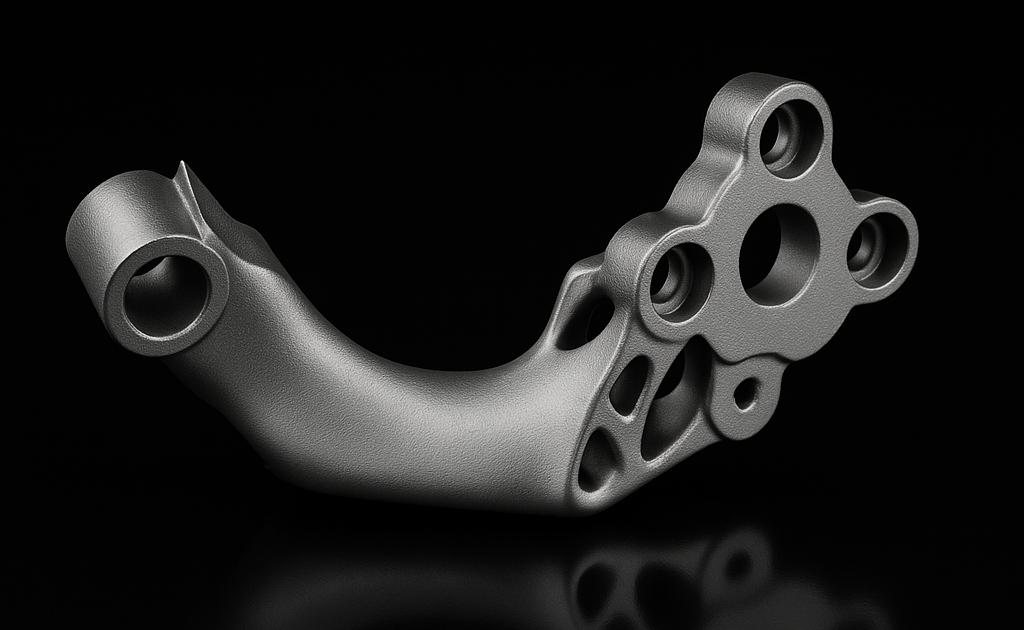
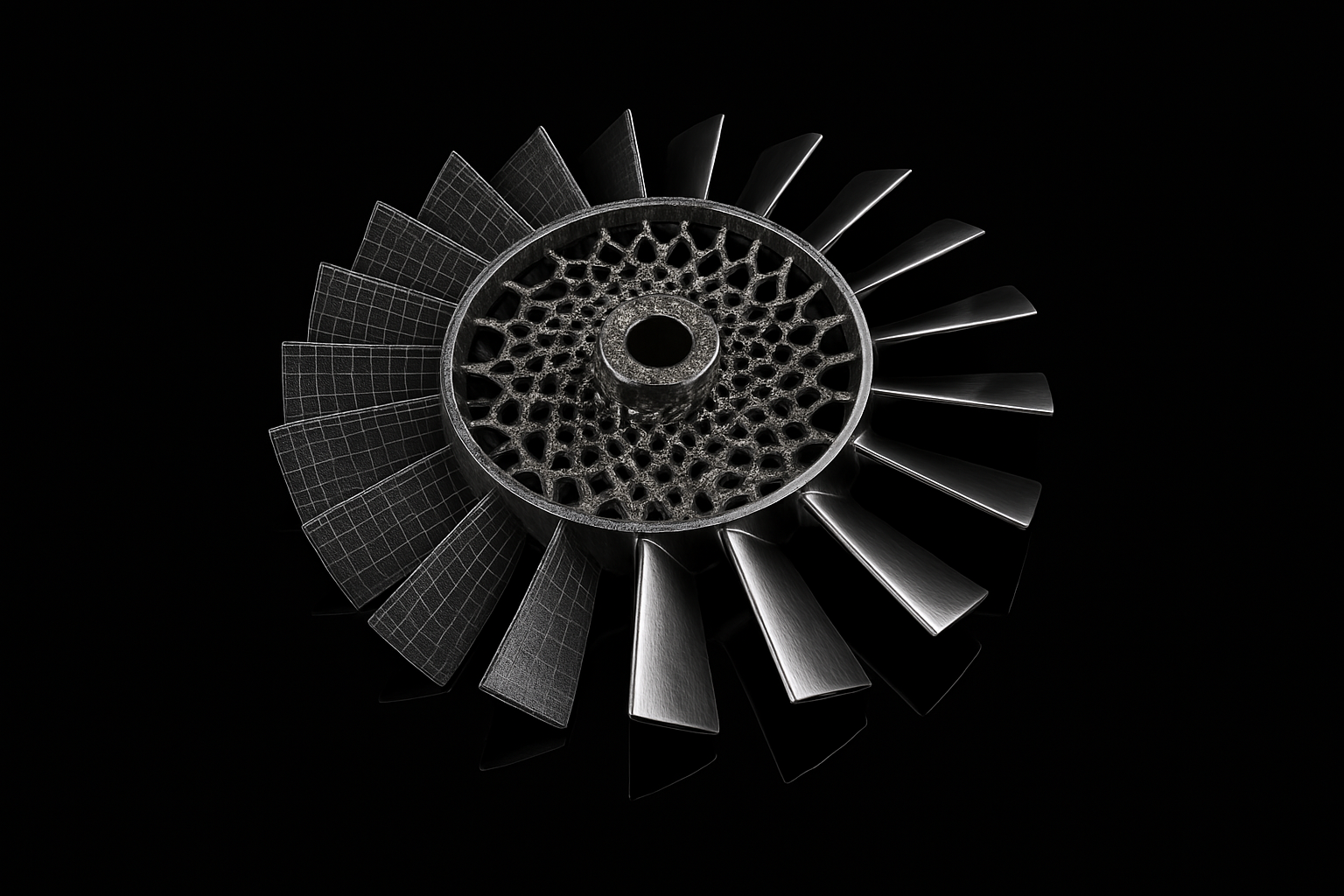
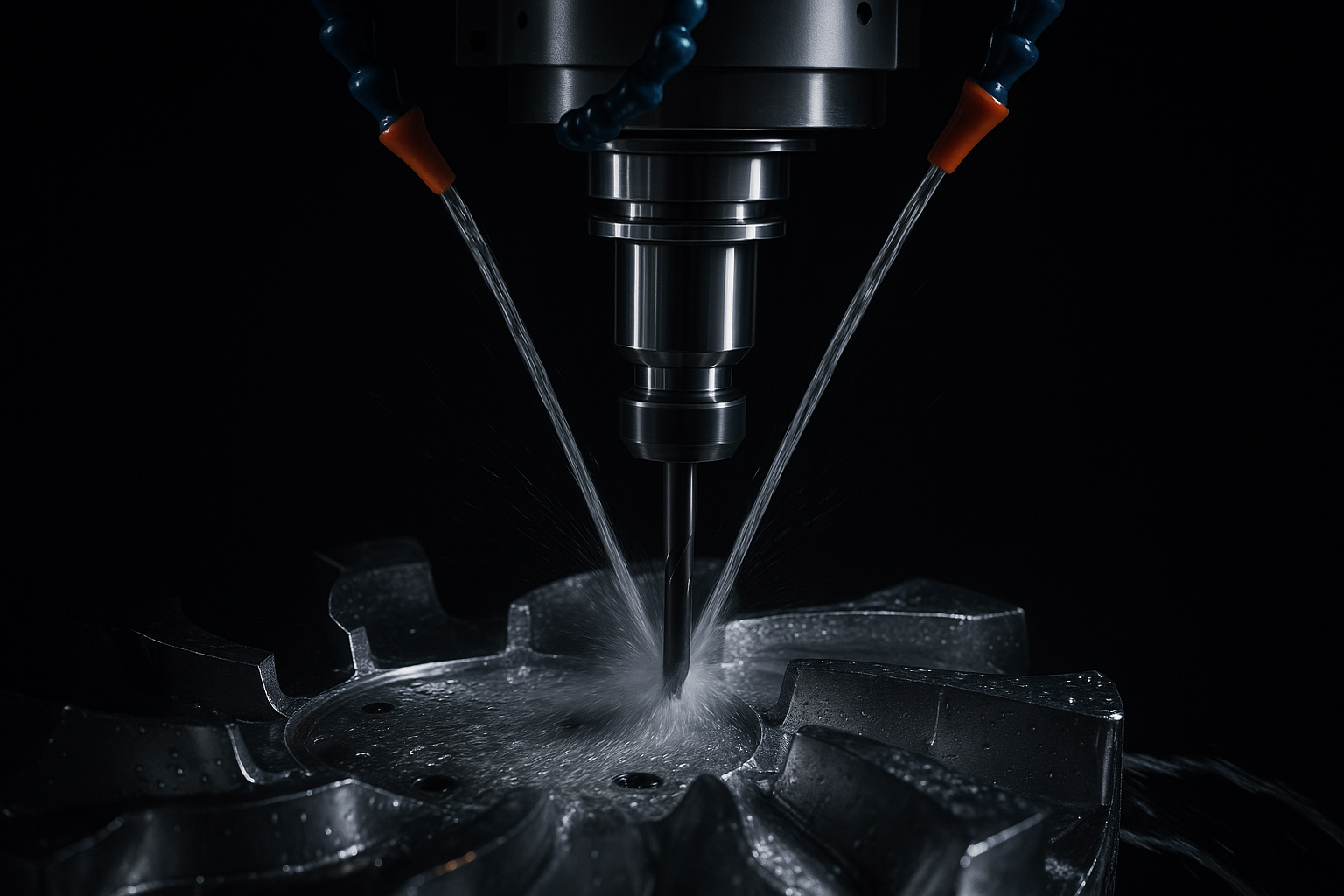
More Than Manufacturing
From concept to production, we provide end-to-end metal 3D printing services to meet your manufacturing needs.
Discover & Scope
We review your CAD, target specs, and cost drivers.
Prototype & Validate
Rapid LPBF builds plus HIP, machining, and full test reports.
Scale & Deliver
Locked process, recurring builds, and on-demand inventory.
Introducing the Omnifusion3D Printer
Developed by Schaeffler, the Omnifusion3D represents the next generation in multi-material additive manufacturing
Unique Capabilities
- •Precision laser fusion with unprecedented accuracy
- •Advanced material compatibility for unique combinations
- •Innovative functional integration in products & tools
- •Flexibility in form for individual, free design
- •Reduced lead time, especially for tools & prototypes
Multi-Material Advantages
In many areas, additive manufacturing has established itself as an alternative to conventional production methods. Multi-material 3D printing opens up almost unlimited possibilities, offering:
- •Simplified production of components with complex geometries
- •Reduced material consumption and waste
- •Increased energy efficiency in production
- •More environmentally friendly material options
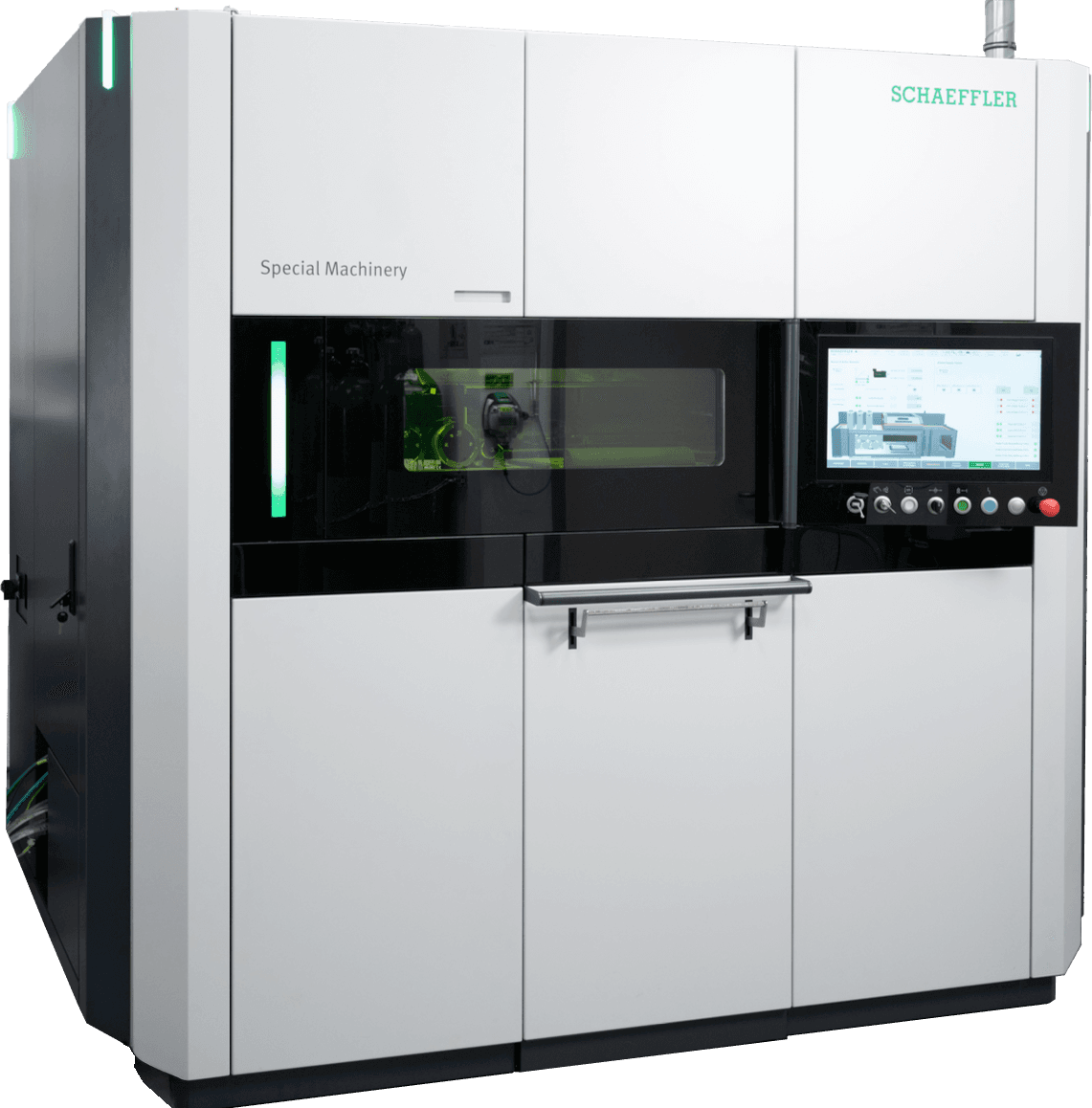
Technical Specifications
Specification | Details |
---|---|
Deposition width | 250 mm / 4.53 inches |
Layer thickness | 40 µm - 150 µm |
Recoating speed | Up to 50 mm/s / 1.97 inches/s |
Integrated powder containers | 750 ml per drum (3 drums) |
Recoater size | 480 x 361 x 182 mm / 18.9 x 14.2 x 7.2 inches |
Powder pixel resolution | 300μm for recoater and die filling platform |
Omnifusion3D Applications
Tool Components
Injection molding insert
- • High thermal conductivity
- • Fast availability of near-end-shape semi finish
- • Low waste of tool material
Welding brackets
- • High wear resistance and thermal conductivity
- • Minimal material waste
Products
Heat sink
- • Organic structure
- • High surface area for improved cooling
- • High thermal conductivity with lightweight housing
Medical implants
- • Innovative joint materials
- • Right material at the right place
Prototypes
Hydrogen applications
- • Increased integration level
- • Reduction of precious materials
- • Controlled porosity
Electric motor coil
- • Fully flexible design
- • Fast component availability